|
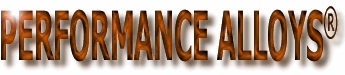
...World Wide Distributor of Beryllium-Free
Copper Alloys...
Manufacturer of Standard &
Custom Components

Site
Updated Often! To ensure proper viewing please Refresh page &
MAKE SURE YOUR BROWSER
IS SET TO UPDATE AT EACH VISIT

|
Performance
Alloys in Motorsports MoldStar® Copper Alloys entered the High
Performance Motorsports market back in 1999. Since introduction, MoldStar® Copper Alloys
have been gaining steadily in popularity because of the success. MoldStar® alloys
are the materials that will endure the widest range of combustion temperatures, shows
compatibility with the widest array of mating materials/coatings and are compatible
with the broadest range of motor fuels. MoldStar® copper alloys have found homes with
winning teams in all motorsport racing sanctioning bodies, classes and vehicular/engine
platforms. Typically MoldStar® alloys are used in "high end" racing
applications being offered by racing component manufacturers by "request only"
and not currently a "catalog offering". So ASK your component
supplier for MoldStar® Alloys by name! Obviously, we cannot name all the
teams and cars that utilize our MoldStar® alloys, but we can surely say "at any
given event we are rarely not in the "Winners Circle".
For Extreme/High Performance as well as OEM applications, MoldStar®
copper alloy valve seats have become the market leader, setting
new standards for diesel and gasoline engines, including
lead-free fuel, E85, and for LPG/CNG and
LNG applications. MoldStar® copper alloys
provide the best combination of thermal conductivity and wear life when
compared to any other product offered in the market. Even when other
manufacturers say their products beat or compare, there is frankly no
better, and no comparison! |
Unleaded Racing Fuels.
When NASCAR® made the rule change requiring the use of "unleaded fuel",
many teams found that the unleaded fuel formulation caused considerable
valve seat deterioration. The NASCAR® teams already running the
MoldStar®90 material, which had already been running for other reasons,
did not see any problems with the MoldStar®90 seats with the change in
fuel formulation. Questions spread quickly among the NASCAR® teams, "why
are we having problems and other teams are not?" The answer clearly was
the teams that were not having problems had already been running
MoldStar®90 as the valve seat material. |
|
Valve Manufacturers and "Performance Enhancing"
Coatings
Many manufacturers of valves for racing are making changes in their manufacturing
processes. The intent is of coatings to add durability to the valve stem and seat angle
without adding weight. The application of coatings such as DLC (Diamond Like Coating) or
PVD (Pressure Vapor Deposition) along with many other "branded" coatings is done
to add wear resistance in combination with reducing friction. With these changes to the
valves, so have come some new hurdles with valve seat and valve guide wear, resulting in
less than anticipated performance and wear life.MoldStar®90 Wear
Resistance against Coated Valve Seat Faces and Stems: MoldStar®90 has proven to
be the material of choice in combination with ANY of the surface treatments currently
being used or offered in the market. Applications have shown that MoldStar®90 materials
form a microscopic surface layer of super hard "nickel-silicides" that is the
result of heat and impact during the operation of the valve train. The longer the
MoldStar®90 seats run, the more durable and harder the seat angle contact surface gets,
without becoming brittle.
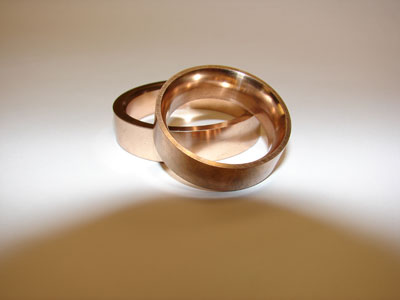 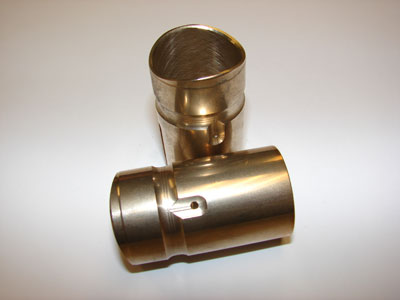
(Moldstar®90 Valve Seats & Moldstar®22 Lifter
Bushings) |
|
WE CAN HELP! We invite you to utilize the free
service of Performance Alloys to help in the selection of the grade of MoldStar® alloy
material for your specific application in Motor Sport. If we cannot help with
one of our products, we will tell you that too!!!!!!!! |
Broadest Range of Compatibility with Motor and Racing
Fuels Applications have proven MoldStar®90 to be compatible and non-reactive
when used in applications with Leaded, Un-Leaded, Alcohol, Nitro
methane, Diesel and
Bio-Diesel motor fuels. Our MoldStar®90 is even used in the production and transmission
by major Petrochemical Producers. |
|
MoldStar®22 is a
"premium" copper alloy from the aluminum bronze family of alloys. This
alloy is an outstanding choice with a proven "track record" for both Lifter
Bushings and Valve Guides. MoldStar®22 copper alloys resist frictional wear, due to the
low coefficient of friction in combination with roller and flat tappet lifters. In
addition to providing wear resistance, low ductility, high hardness and toughness of the
MoldStar®22 alloy also resists mis-shaping or ovality due to high spring pressures and
extreme travels of the valve train. |
Still using Cast Iron Valve
Seats or not exactly sure which seats Cylinder Head Assemblers/Manufacturers
use? Believe it or not when we talk to the manufacturers or assemblers of
cylinder heads for racing or other performance applications, there is a surprising array
of misinformation combined with some amazing folklore that seems to be the basis for the
selection of the valve seat material. CONTACT US TO LEARN THE FACTS! |
What Material is your Component supplier using?
Commercial Bronze Alloys in Racing Applications. The fact is many component
manufacturers use Bronze Alloys considered by the Primary Metal Industry as
"low grade or commercial" brass or bronze. This is typically due to availability
combined with low cost. Regardless of claims by some component manufacturers, it is
unlikely any of them are using their own "formulation". This is because cost for
"special or custom" formulated copper alloys would be absolutely out of
proportion considering the sell price of the component. DO YOU REALLY WANT
THE CHEAPEST/LOW GRADE MATERIAL ON THE MARKET IN YOUR RACE ENGINES OR IN YOUR COMPONENTS? |
|
HARDNESS
This is one of the more misunderstood and misrepresented phenomenon with copper alloys.
Most copper alloys offer high thermal conductivity, high mechanical strength and hardness
are from a family of metals considered to be precipitation hardening materials.
Another term used to define this heat treatment is an aging process. The specific
aging processes are based on the copper alloy chemistry, which when aged in a controlled
environment, determines the alloy hardness. In addition to affecting the chemical
structure, the aging process also yields controlled levels of thermal and electrical
conductivity. Precipitation hardening is done by heating an alloy to a specific
temperature, then holding at that temperature for a predetermined period of time, then
air-cooled. For stability reasons aging is done only after a solution annealing process.
This means that the alloy properties are changed when exposed to time and temperature
while in useby welding, surface treatments or some incident that heats the component
to a temperature above the original aging temperature. Exposure to time and relative
temperatures over the original aging temperature for a specific alloy can either increase
or decrease the properties of the alloy. An occurrence called over aging can
seriously affect the short and long-term performance of copper alloy mold components. |
Over aging also can soften materials to surprisingly low levels, where
the components will fail because of lack of expected hardness. Or, over aging can reduce
elongation and ductility to the point where the component fractures because it is too
brittle for an application. Copper alloys, like steels, provide the most desirable
performance characteristics at optimum hardness rather than ultimate
hardness.
Some alloy manufacturers provide products at the ultimate hardness in efforts to entice
buyers with the highest hardness products. While other manufacturers provide
products at the optimum, which in effect allows for the slight increase in hardness and
lower ductility as a result of continued aging. Providing products at the ultimate
hardness is a disservice to users because the ductility of the product is
lowgenerally 3 percent elongation or less, which when used and exposed to ongoing
time and temperature, exhibit even less ductility and eventually fail due to fracture. If
someone told you that after running a mold 24/7, your components made of a copper
alloychosen because it was 38-40 Rockwell Cwould start fracturing
like glass, would you believe them? Those that dont soon find out that the copper
alloys at 30 Rockwell C are the superior choice and will yield the longest
lasting components. In other words, buyer beware of copper alloys offered at or near 40
Rockwell C. |
Like everything else in life. The lower the cost, the further
back in the line-up you are and less visible you are. This is absolutely no more evident
than in professional racing and with their sponsors. GET VISIBLE. It's worth it. |
Get out of the CHEAP SEATS, be part of the
real action and enjoy the view from the FRONT ROW . Use MoldStar® Copper Alloys! |
|
Acknowledgements of Trademarks: the "mark" NASCAR® is owned by
the National Association for Stock Car Auto Racing, Inc., the "mark" MoldStar®
is owned by Performance Alloys and Services, Inc. |
|
Performance Racing |
Click here
to download the Moldstar®90 Racing Information
Click here to download the
Moldstar®22 Racing Information
Click here to download the
Moldstar® Services for Racing
Download time will depend on your connection speed. |
SITE INDEX
|
Disclaimer
While the information contained is deemed reliable, no warranties are expressed or
implied. For specific information regarding an application please call 1-800-272-3031 or
e-mail us at sales@moldstar.com
|
Copyright © 2024 by Performance Alloys &
Services, Inc
Web site hosted by Network Solutions
All Rights Reserved.
|
|